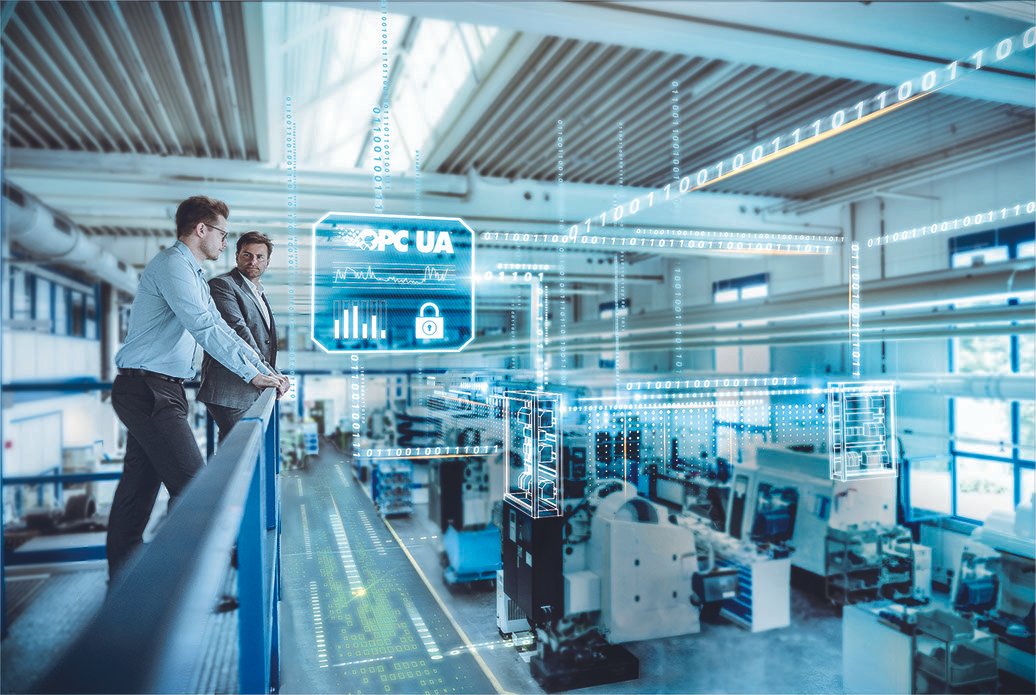
The KEY to Unleasing Maximum Efficiencies and Profitability is…
-Systematic Thinking-
Systematic thinking (the opposite of localizing improvement - “sub-optimizing”) is what transforms factories—it’s the secret to turning potential into performance. With 30+ years refining this approach, I’ve blended Lean, Theory of Constraints, and MOS into a method that streamlines operations, clears bottlenecks, and lifts P&L for lasting results. My journey’s led to a system equity groups and manufacturers rely on—explore it here, from free tools to proven strategies, and see what it can do for you
Michael Sutherland
A seasoned manufacturing leader with 30+ years transforming small to mid-sized factories worldwide—U.S., Mexico, Europe, Asia—I’ve honed a knack for turnarounds that boost profitability and build standout teams. Rooted in Lean, Theory of Constraints, and MOS, my approach drives efficiency and growth through hands-on leadership and collaboration. Equity groups, manufacturers, and stakeholders count on me to deliver value—whether reviving operations or mentoring talent for the long haul.
A Three Part Process for Step Function Improvement
Merge Lean Manufacturing with the Theory of Constraints,
Implement a Robust Management Operating System,
and Develop a Passionate Team
To Unleash Capacity, Throughput and Margin!
A Quick Overview…
Lean Manufacturing
Lean Manufacturing is the art of doing more with less—stripping away waste to reveal a sharper, faster operation. It targets the silent drains—overproduction, idle stockpiles, redundant steps—and turns them into fuel for efficiency. I’ve used it to breathe new life into sluggish production floors, guiding teams to rethink every move and deliver what customers truly value. It’s not just about cutting corners; it’s a disciplined shift that reshapes processes, boosts profitability, and sets the stage for growth that sticks.
Theory of Constraints (TOC)
The Theory of Constraints (TOC) is a spotlight on the single snag that slows everything down—the bottleneck holding back the full flow of results. It zeros in, lifting that limit to unleash capacity, driving more sales with minimal cost input. I’ve applied TOC to crank up output where others saw gridlock, mentoring teams to break the choke point and unlock hidden potential. It’s a focused, no-nonsense approach that transforms a struggling system into a steady stream of performance and profit.
Management Operating Systems (MOS)
A Management Operating System (MOS) is the backbone of disciplined execution—a framework that aligns goals, metrics, and actions across an organization. It’s the pulse check that keeps teams on track, blending real-time data with clear priorities to drive decisions. I’ve implemented MOS to turn scattered efforts into a unified push, ensuring every level moves in sync toward excellence. It’s the glue that ties strategy to results, creating a steady rhythm of accountability and progress.
Developing a Performance-Driven Team Culture
Building a team culture driven to perform is about igniting a shared hunger for excellence—aligning every member to chase results with purpose. It’s forging a crew that thrives on accountability, fueled by clear goals and hands-on mentoring. I’ve shaped teams to outpace expectations, turning raw talent into a cohesive force that executes flawlessly under pressure. This isn’t just motivation—it’s a crafted mindset where collaboration and discipline collide, propelling the entire operation toward standout success.
Combining Lean and TOC: Next-Level Performance
Blend Lean’s waste-cutting edge with TOC’s bottleneck-breaking focus, and you unlock a powerhouse—a hyperfocus on the whole system that explodes benefits fastest. TOC clears the path for maximum flow while Lean enables the throughput to flow unabated, creating a seamless, unstoppable operation. I’ve led teams to harness this combo, driving rapid turnarounds that lift margins, accelerate growth, and deliver significant value. It’s the ultimate one-two punch for transforming manufacturers into lean, high-output winners.
Explore the resources below to begin analyzing your operation.
Use them to get a feel for what’s possible—I’m here when you’re ready to take the next step.
Article: Read a Plant—Faster: Lean Flow, Throughput Power, and a Fully Optimized System
A Nod to R. Eugene Goodson and Eli Goldratt
This article describes my journey to cracking the code of factory transformation—a path that started with the insights of Read a Plant Fast and evolved into a powerful system blending Lean, Theory of Constraints, and a strong Management Operating System (MOS.) What began as a quest to assess operations in a heartbeat grew into a practical trifecta: Lean strips waste, TOC breaks bottlenecks, and the MOS cements lasting gains. Together, they turn struggling plants into profit engines—here’s how I got there, and why it’s the key for anyone aiming to revive an asset or reshape their P&L. Read it to to see if it makes sense to you, and begin your assessment with the provided materials. Click HERE to read the original article: Read a Plant Fast by Eugene Goodson
The Theory of Constraints: A Primer
Discover how Theory of Constraints (TOC) transforms factories by targeting bottlenecks—those silent barriers to profit. Inspired by The Goal (by Eli Goldratt), this primer unpacks Alex Rogo’s journey from chaos to cashflow, revealing a 5-step process to unlock flow and lift P&L. It’s a practical guide for any operation—showing how to spot constraints, break them, and drive results fast. Whether you’re streamlining production or rethinking efficiency, this resource offers clear, actionable insight into TOC’s power. Dive in to learn what’s holding you back and how to move forward—more tools await to build on it
Another Primer: Lean Manufacturing
Understand Lean Manufacturing with this Lean Primer—a deep dive into cutting waste to boost profit. Born from Toyota’s flow-driven system, it unpacks the 5 Principles and key tools like Value Stream Mapping to transform factories from chaos to clarity. Lean strips excess—overproduction, defects, delays—unlocking efficiency and P&L gains. More than waste-cutting, it’s a return to Lean’s original flow focus, complementing TOC perfectly. Ideal for any operation aiming to streamline and grow—download to explore, apply, and see results. More tools await to take it further.
Why Lean and TOC Are Soulmates
Unlock the real Toyota Production System with this Lean-TOC Combo Cheat Sheet. Lean cuts waste, TOC aligns the system—together, they revive TPS’s flow-first power, not just waste hunts. Learn why Lean alone can flop on the P&L and how RABIT—Rapid Bottleneck Improvement Team—hyperfocuses resources for profit. This quick guide blends the best of both, showing how to turn chaos into cashflow fast. Ideal for any operation craving efficiency and gains—download to see the system Ohno built, reborn.
Get Started - 20 Questions to Assess
Stagnation kills profit—the Operational Snapshot Tool snaps a clear picture of your factory’s health in minutes. A dance of deliberate moves—execs to floor—it spots bottlenecks, waste, and drift. Built from decades of turnarounds, these 19 questions reveal gaps to your desired state (flow, profit, alignment), guiding intentional, P&L-driven ops. Perfect for assessing ops or acquisitions—download, walk your plant, see where profit hides. Pairs well with the above TOC Primer, Lean Primer, and Lean-TOC Combo discussion.
Overview Presentation - The Throughput Production System
Unlock the power of throughput with Intro to TOC - The Throughput Production System. This PowerPoint dives into the Theory of Constraints (TOC), showing how to boost flow and profit by targeting bottlenecks—fast. Packed with real-life examples from decades of turnarounds, it reveals why throughput trumps busywork, transforming factories for equity wins or operational leaps. Ideal for leaders eyeing P&L gains—download to see TOC in action.
These tools—TOC, Lean, and beyond—can help you unlock your factory’s potential.
Begin with a single step, spot the gaps, and chart your progress. Ready to transform insight into action? My decades of turnaround expertise are just a click away! Let’s make your operation thrive! If it would help, ask about a no obligation strategy discussion!
Verified Results of the Combined System
Machine Shop
30% Throughput Improvement
40% Inventory Reduction
10% Footprint Reduction
15% Labor Reduction (attrition)
20 bps Margin Improvement
Sheet Metal Shop
22% Throughput Improvement
31% Inventory Reduction
5% Footprint Reduction
10% Labor Reduction (attrition)
15 bps Margin Improvement
Subassembly Shop
65% Throughput Improvement
32% Inventory Reduction
10% Footprint Reduction
20% Labor Reduction (attrition)
45 bps Margin Improvement